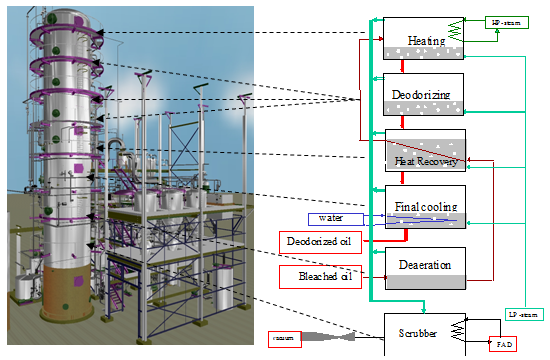
در این مقاله به مبحث بی بو سازی روغن می پردازیم:
در مراحل اولیه رشد و توسعه صنعت روغن ها و چربی های خوراکی، حمله عطر و طعم های نامطبوع یک مشکل بسیار بزرگ محسوب می شد. لارد و کره به همان شکلی که تولید می شد مصرف می شدند و طعم های طبیعی به عنوان یک ویژگی باارزش در نظر گرفته می شد. روغن زیتون، که یکی از قدیمی ترین روغن های نباتی شناخته شده بود، بخاطر طعم خاص و متمایزش کاربرد زیادی داشت و دارد.
با این حال رشد و توسعه سریع زمین های کشت پنبه در اواخر قرن ۱۹ منتج به تولید مقادیر زیادی روغن پنبه دانه شد، که یک انگیزه اقتصادی برای استفاده از این روغن نباتی را به وجود آورد. روغن پنبه دانه رنگبری شده و تصفیه شده تند و تیز، به عنوان یک روغن طبخ یا سالاد پیشنهاد شد و با تلو یا استئارین اولئین به عنوان یک جایگزین لارد مخلوط می شد.
این محصولات از لحاظ قیمت به لارد و روغن زیتون برتری داشته اما طعم ناخوشایند آن ها بسیار شدید بود بطوریکه پذیرش ضعیفی توسط مصرف کننده داشت. علاوه بر آن جهت سفت کردن روغن های نباتی که باعث ایجاد یک عطر و طعم نامطبوع تری در روغن می شدند، توسعه داده شد.
تلاش های صورت گرفته در جهت از بین بردن عطر و بو ها به روش شیمیایی یا پوشاندن آن ها با ادویه جات یا طعم ها، موفقیت آمیز نبودند. اولین تلاش موفقیت آمیز در از بین بردن عطر و بوهای نامطبوع یک چربی یا روغن شامل تزریق بخار زنده بداخل یک روغن در دماهای بالا بود.
این پروسه بهبود طعم در انگلستان کشف شد اما به زودی توسط اکثر تولید کنندگان امریکایی چربی و روغن تعدیل شد.
مزایای تیمار کردن روغن ها با بخار به منظور از بین بردن عطر و طعم نامطبوع در اوایل دهه ۱۸۹۰ توسط Henry Eckstein شناسایی گردید. David Wesson این پروسه را با استفاده از دماهای بالاتر و حفظ روغن تحت خلاء درحین دمیدن با بخار فوق گرم (سوپرهیت) اصلاح نمود.
بی بو سازی پروسه تقطیر روغن در خلاء-بخار در دمای بالا بوده که در طول آن FFAها و مقادیر ناچیز مواد بدبو از بین رفته و یک روغن شیرین و مطلوب و بدون بو حاصل می شود.
اکثر روغن های نباتی عطر و طعم خاص نامطلوب خود را حفظ می کنند و در طول فراوری عطر و طعم های دیگری نیز بدست می آورند.
رنگبری یک عطر و بوی خاکی مانند را به روغن می دهد و هیدروژناسیون نیز یک عطرو طعم نامطبوع خاصی را در روغن ایجاد می کند. مواد بدبو FFAها، آلدهیدها، کتون ها، پروکسیدها، الکل ها و دیگر ترکیبات آلی می باشند.
علاوه بر آن رنگدانه های کاروتنوئیدی خاصی نیز تجزیه شده و منتج به یک اثر رنگبری در نتیجه حرارت می شود. حذف موثر و کارامد این مواد بستگی به فشار بخار اعمال شده، داشته که برای یک جزء اصلی معین، تابعی از دما بوده و با دما افزایش می یابد.
بی بو سازی آخرین مرحله فراوری اصلی می باشد که در طی انجام آن طعم و بو و بسیاری از صفات کیفی پایداری یک روغن می تواند تحت تاثیر قرار بگیرد. از این نفطه نظر، تلاش هایی در جهت حفظ کیفیت روغن های بی بو شده، صورت گرفته است. ازینرو توجه بسیار زیادی باید به انتخاب، عملیات اجرایی و نگهداری و تعمیرات تجهیزات بی بوکننده و شرایط عملیاتی داده شود.
متغیرهای عملیاتی
شرایط بی بو سازی به نوع روغن، کیفیت روغن و سیستم تصفیه مورد استفاده، بستگی دارد. یک تغییر در تکنولوژی تصفیه در جهت تصفیه فیزیکی که در آن FFA منحصرا بوسیله تقطیر با بخار حذف می شود نیاز به اعمال شرایط شدیدتری در مقایسه با روغن های تصفیه شده به روش شیمیایی دارند.
با استفاده از تصفیه شیمیایی، بیشتر محتوای FFA قبل از بی بوکردن خنثی می شود. محتوای FFA در روغن های تصفیه شده به روش فیزیکی، در مقایسه با محتوای ۰٫۰۵ تا ۰٫۱ درصدی برای تصفیه شیمیایی، بین ۱٫۰ و ۵٫۰ درصد می باشد. نیاز بخار تقطیر برای روغن های تصفیه شده به روش شیمیایی و فیزیکی می تواند با تغییر یک یا بیش از یک متغیر عملیاتی، بدست آید. ۴ متغیر عملیاتی مرتبط که بر کیفیت روغن بی بوشده تاثیر می گذارند شامل خلاء، دما، سرعت عاری سازی بخار و زمان نگه داشتن در دماهای بی بو کردن می باشد.
خلاء
اگر اسیدهای چرب و ترکیبات بدبو قرار است در پایین ترین دمای ممکن تقطیر شود، تقطیر بایستی در فشارهای مطلق پایین درنتیجه اعمال سیستم خلاء انجام شود. نقطه جوش اسیدهای چرب و فشار بخار مواد بدبو با کاهش فشار مطلق، کاهش می یابد.
فشار مطلق پایین مورد نیاز، که معمولا بین ۲ و ۴ mbar بوده، معمولا بوسیله سیستم های خلاء شامل ترکیبی از اجکتورهای جت بخار، کندانسورهای بخار و پمپ های مکانیکی خلاء حاصل می گردد.
سیستم های ویژه خلاء برای بدست آوردن فشارها و هزینه های عملیاتی پایین تر و به طور همزمان کاهش مواد منتشر شده بوسیله کندانس موثرتر ترکیبات فرّار طراحی و توسعه داده شده اند.
در سیستم های کندانس خشک، بخار پاشش شده بر روی سطح کندانسورهایی که به طور متناوب کار می کنند کندانس می شود. مواد غیرقابل کندانس باقیمانده بوسیله پمپ های مکانیکی یا با استفاده از یک سیستم اجکتور خلاء حذف می گردد.
دما
دماهای بی بو سازی بایستی به اندازه کافی بالا باشد تا فشار بخار ناخالصی های فرار در روغن را به راحتی بالا ببرد. فشار بخار مواد بدبو با افزایش دمای چربی سریعا افزایش می یابد.
به عنوان مثال فشار بخار اسید چرب پالمیتیک ۱٫۸ mm در ۳۵۰ درجه فارنهایت (۱۷۶٫۷ درجه سانتیگراد)، ۷٫۴ mm در ۴۰۰ درجه فارنهایت (۲۰۴٫۴ درجه سانتیگراد)، ۲۵٫۰ mm در ۴۵۰ درجه فارنهایت (۲۳۲٫۲ درجه سانتیگراد) و ۷۲ mm در ۵۰۰ درجه فارنهایت (۲۶۰ درجه سانتیگراد) می باشد.
با فرض اینکه رابطه دما-فشار بخار برای تمامی مواد بدبو مشابه با این رابطه برای اسیدچرب پالمیتیک می باشد، هر ۵۰ درجه فارنهایت (۸/۲۷ درجه سانتیگراد) افزایش دمای بی بوکننده سرعت حذف مواد بدبو را سه برابر می کند.
یا به بیان دیگر مدت زمانی که برای بی بوکردن یک روغن در دمای ۳۵۰ درجه فارنهایت طول می کشد ۹ برابر مدت زمانی است که در ۴۵۰ درجه فارنهایت به طول می انجامد. دماهای بالاتر بی بوکننده، قطعا مدت زمان های بی بو کردن کوتاهتری را در پی خواهد داشت؛ با این وجود دمای بیش از حد منتج به پیشرفت پلیمریزاسیون، ایزومریزاسیون و در نتیجه تولید اسیدهای ترانس، ترک خوردگی حرارتی با تشکیل ترکیبات بدبو و محصولات با نقطه جوش پایین، برگشت رنگ و تقطیر توکوفرول ها می شود.
به طور کلی تشکیل اسیدهای ترانس در طول بی بوکردن در کمتر از ۴۲۸ درجه فارنهایت (۲۲۰ درجه سانتیگراد) قابل چشم پوشی بوده، بین ۴۲۸ و ۴۶۴ درجه فارنهایت (۲۲۰ و ۲۴۰ درجه سانتیگراد) معنی دار بوده و در بالاتر از ۴۶۴ درجه فارنهایت (۲۴۰ درجه سانتیگراد) تقریبا به صورت نمایی می شود.
تجزیه گرمایی توکوفرول ها در دماهای بالاتر از ۵۰۰ درجه فارنهایت (۲۶۰ درجه سانتیگراد) در پروسه بی بو کردن قابل توجه می باشد. مشخص شده که دردمای ۵۲۵ درجه فارنهایت (۲۷۵ درجه سانتیگراد) در مقایسه با ۴۶۵ درجه فارنهایت(۲۴۰ درجه سانتیگراد) دو برابر توکوفرول ها و استرول ها از بین می روند و اینکه تغییرات فشار از ۲ تا ۶ میلی بار تنها یک اثر مختصری بر عاری سازی توکوفرول/استرول دارد.
همچنین عملیات بی بو کننده در دماهای بالا می تواند باعث پیشرفت تجزیه گرمایی برخی اجزاء اصلی طبیعی روغن همچون پیگمان ها و برخی مقادیر ناچیز کمپلکس های فلز-پرواکسیدان شود. پیگمان های کاروتنوئیدی در بی بو کردن که با دمای ۴۴۶ درجه فارنهایت (۲۳۰ درجه سانتیگراد) آغاز می شود، تجزیه شده و از بین می رود. بنابراین بایستی بین زمان و دمای بی بو کردن روغن ها و چربی های خاص یک سازگاری برقرار گردد.
دماهای اپتیمم عملیاتی بی بوکننده، از محصولی به محصول دیگر متفاوت است. به طور کلی، چربی های حیوانی در مقایسه با روغن های نباتی به شرایط ملایمتری نیاز دارند.
بی بو کردن روغن های تصفیه شده به روش شیمیایی، بموجب مقادیر کمتر FFA و حذف موثرتر ترکیبات قطبی، محصولات اکسیداسیون و پیگمان ها آسانتر از روغن های تصفیه شده به روش فیزیکی می باشد.
در میان روغن های نباتی، آن روغن هایی که حاوی اسیدهای چرب با زنجیره نسبتا کوتاهتر می باشند همچون روغن های هسته پالم و نارگیل، در مقایسه با روغن های خانگی (domestic oil) تشکیل شده از اسیدچرب های با زنجیره بلندتر، نیاز به دماهای پایین تری برای بی بوکردن دارند. بی بوکردن روغن های هیدروژنه شده بخاطر محتوای FFAی بالاتر و یک بوی متمایز ایجاد شده توسط واکنش هیدروژناسیون، معمولا مشکل تر است.
روغن های ذرت معمولا برای بدست آوردن رنگبری مطلوب با حرارت دهی، نیاز به دمای بالاتر یا زمان ماند طولانی تر دارند. به طور کلی، دماهای بی بوکردن از ۴۰۰ تا ۴۷۵ درجه فارنهایت (۲۰۴ تا ۲۴۶ درجه سانتیگراد) و در برخی موارد تا ۵۲۵ درجه فارنهایت (۲۷۴ درجه سانتیگراد) متغیر می باشد.
بخار عاری سازی (دفع)
همراه با دما و فشار در بی بوکننده، بخار عاری سازی کافی مورد نیاز می باشد.
مقدار بخار عاری سازی مورد نیاز، تابعی از فشار مطلق عملیاتی و راندمان اختلاط طرح تجهیزات می باشد.
هم زدن روغن، که برای قرار دادن مداوم سطوح جدید روغن در معرض فشار مطلق پایین، ضروری می باشد، با استفاده از بخار عاری سازی کاملا پراکنده شده انجام می شود.
بنابراین عمق روغن، فاکتور اولیه برای تعیین مقدار بخار مورد نیاز برای عاری سازی و بی بوکردن یا زمان نگه داشتن می باشد.
مقدار اسیدهای چرب تقطیر شده با هر پوند بخار مستقیما با فشار بخار اسیدهای چرب متناسب می باشد. عاری سازی یا دفع موثر با بخار بستگی به حجم دارد؛ به عنوان مثال عملیات در ۱ میلی بار، در مقایسه با عملیات ۶ میلی باری، به درصد وزن مولکولی پایین تری از بخار عاری سازی نیاز خواهد داشت.
اختلافات میان منبع های روغنی نیز بر مقدار بخار مورد نیاز تاثیر دارد؛ به عنوان مثال، از بین بردن بوی روغن کنولا در مقایسه با روغن سویا نیاز به بخار بیشتری خواهد داشت.
بخار زنده بیش از اندازه سبب هیدرولیز و افزایش مصرف انرژی برای سیستم خلاء می شود.
شرایط معمول عاری سازی با بخار در بی بوکردن برای روغن های تصفیه شده شیمیایی ۵ تا ۱۵ wt% برای سیستم های بچ و ۰٫۵ تا ۲% برای سیستم های بی بوکننده پیوسته و نیمه پیوسته می باشد.
زمان نگه داشتن یا هولدینگ
زمان هولدینگ بی بوکننده، دوره ایست که در آن چربی یا روغن در دمای بی بوکردن و در معرض بخار عاری سازی قرار دارد.
زمان عاری سازی برای بی بوکردن موثر بایستی به اندازه ای باشد که ترکیبات بدبوی چربی ها و روغن ها تا سطح مورد نیاز کاهش یابند.
این مدت زمان با طرح تجهیزات تغییر خواهد کرد.
به عنوان مثال یک بی بوکننده بچ با عمق روغن ۸ تا ۱۰ فوت بالاتر از توزیع کننده بخار پاششی، برای بی بوکردن نیاز به مدت زمان طولانی تری در مقایسه با یک سیستم پیوسته یا نیمه پیوسته که لایه های سطحی روغن را تیمار می کند، دارد.
به طور معمول زمان هولدینگ در دماهای بالا برای سیستم های بی بوکننده بچ، ۳ تا ۸ ساعت بوده در حالیکه زمان هولدینگ برای سیستم های پیوسته و نیمه پیوسته از ۱۵ تا ۱۲۰ دقیقه متغیر است.
علاوه بر آن، واکنش های خاص با روغن های بی بو شده، با ازبین رفتن FFAها ارتباطی نداشته اما در عوض به تولید یک روغن پایدار بعد از بی بوکردن کمک می کند.
این واکنش ها و رنگبری حرارتی وابسته به زمان و دما می باشد. بنابراین سیستم های بی بوکردن، یک دوره نگهداری در دماهای بی بوکردن به منظور انجام این واکنش ها و ایجاد رنگبری توسط حرارت را فراهم می کند.
سیستم های بی بوکردن
تجهیزات بی بوکردنی که هم اکنون مورد استفاده قرار می گیرد، می تواند به سه گروه اصلی طبقه بندی شود: بچ، کانتینیوس و نیمه کانتینیوس. انتخاب سیستم بستگی به چند فاکتور اعم از تعداد تغییرات فیداستاک، بازیابی حرارت، سرمایه گذاری، هزینه های عملیاتی، نیازهای اکولوژی (بوم شناسی)، تصفیه شیمیایی یا فیزیکی و … می باشد.
بچ
این سیستم اساسا، ساده ترین نوع سیستم بی بوکردن که می تواند نصب گردد، می باشد.
بخش اصلی آن شامل یک ظرف به شکل یک سیلندر عمودی با هدهای قیفی یا گود می باشد. این مخزن باید از استیل ضدزنگ ۳۰۴ ساخته شده تا از فعالیت کاتالیتیک زیان آور مس و آهن بر روی روغن اجتناب شود، و به منظور جلوگیری از نشت هوا باید کاملا جوش داده شده و برای به حداقل رساندن افت حرارتی کاملا عایق بندی شده باشد.
رنج معمول ظرفیت ۱۰۰۰۰ تا ۴۰۰۰۰ پوند بوده، اگرچه اندازه های ۱۵۰۰۰ تا ۳۰۰۰۰ پوندی برای سیستم بچ ترجیح داده می شود. قطرهای ظرف معمولا طوری انتخاب می شود که یک عمق ۸ تا ۱۰ فوت روغن بدهد و هداسپیس با مقدار مشابهی در بالای سطح روغن داشته باشد.
لازم است هداسپیس کافی در نظر گرفته شود تا از افت روغن زیاد در نتیجه چرخیدن و ترشح روغن توسط بخار تزریق شده، جلوگیری شود. بخار عاری سازی به قسمت پایین ظرف از طریق یک توزیع کننده تزریق می گردد.
علاوه بر سیستم اجکتور بخار، تجهیزاتی برای حرارت دهی، خنک کردن، پمپ کردن و فیلتر کردن روغن، مورد نیاز است. ابزارهای کنترل سیستم بچ شامل یک وسیله برای نشان دادن دمای روغن و یک گیج فشار که برای نشان دادن دقیق فشارهای پایین در داخل بی بوکننده، طراحی شده، می باشد.
عملیات واحد در یک دمای بالا و فشار ۶ تا ۱۲ میلی بار، برای یک چرخه بی بوکردن کامل شامل شارژ کردن، حرارت دادن، بی بوکردن، خنک کردن و تخلیه روغن، نیاز به ۸ ساعت زمان دارد.
برخی سیستم هایی که در فشارهای بالا یا دماهای بی بوکردن پایین تر عمل می کنند برای این چرخه به ۱۰ تا ۱۲ ساعت زمان نیاز دارد. مقدار کل بخار مورد نیاز برای عاری سازی، از تقریبا ۱۰ تا ۵۰ پوند به ازاء ۱۰۰ پوند روغن متغیر بوده و کاربرد متوسط آن احتمالا حدود ۲۵ پوند به ازاء ۱۰۰ پوند روغن می باشد.
بخار عاری سازی معمولا در ۳ پوند به ازاء هر ۱۰۰ پوند روغن در هر ساعت در فشار ۶ میلی باری تزریق می گردد. روغن بایستی بعد از بی بو کردن و قبل از اینکه در شرایط اتمسفری تخلیه گردد، تا جایی که عملی باشد خنک گردد تا اکسیداسیون به حداقل برسد.
دمای ۱۰۰ تا ۱۲۰ درجه فارنهایت (۳۸ تا ۴۹ درجه سانتیگراد) برای روغن های مایع ترجیح داده می شود، بطوریکه دماهای بالاتر برای محصولات دارای نقاط ذوب بالاتر لازم می باشد اما باید هنوز تا حد ممکن پایین باشد.
بی بوکردن به روش بچ دارای مزیت سادگی طرح، انعطاف پذیری و سهولت عملکرد می باشد. این سیستم می تواند مطابق با نیاز می تواند در یک دوره کوتاه یا بلند با محصول مکرر و حتی تغییرات شرایط بی بو کردن عمل کند. سیستم های بی بو کننده بچ از لحاظ مکانیکی نیاز به تعمیرات بسیار کمی دارد؛ با این حال هزینه امکانات برای بی بوکردن بچ، به طور قابل توجهی بالاتر از هزینه های مربوط به سیستم های کانتینیوس و یا نیمه کانتینیوس می باشد.
سیستم های بچ ابزار مناسبی برای بازیابی هر بخش قابل توجهی از حرارت مورد نیاز نمی باشد، آن ها دارای مصرف بخار عاری سازی بالایی بوده، نیاز به سیستم های بزرگ خلاء با نیاز بالای آب و بخار دارند. اما، هزینه های ثابت و نیروی کارگری کمتر برای نصب اولیه، می تواند یک بخشی از هزینه های بیشتر مربوط به امکانات را جبران کند.
نیمه مداوم
این سیستم ها براساس کارکردن بچ های محدود روغن در یک ترتیب زمان بندی شده هواگیری-حرارت دهی، هولدینگ-عاری سازی با بخار و خنک کردن عمل می کند به طوریکه قبل از اینکه به مرحله بعدی وارد گردد هر ذره از روغن کاملا در معرض هر یک از شرایط قرار گیرد.
بی بوکننده نیمه کانتینیوس شامل یک پوسته سیلندری شکل بلند از جنس استیل کربن با ۵ یا بیش از ۵ سینی از جنس استیل ضدزنگ ۳۰۴ که داخل پوسته بیرونی، البته نه بسیار نزدیک به هم، قرار گرفته، می باشد.
هر سینی مجهز به یک پاشش بخار بوده و قابلیت نگهداشتن یک بچ مشخصی از روغن را دارد. بوسیله یک تانک اندازه گیری، روغن به سینی بالایی شارژ شده و در آن هواگیری شده درحالیکه با بخار تا دمای حدودا ۳۲۰ تا ۳۳۰ درجه فارنهایت (۱۶۰ تا ۱۶۶ درجه سانتیگراد) حرارت دهی می شود. در انتهای دوره حرارت دهی، بار روغن به طور اتوماتیک به سینی دوم خال شده و سینی بالایی مجددا پر می شود.
در سینی دوم، روغن تا دمای عملیاتی حرارت داده می شود و دوباره بعد از یک دوره مشخصی، به طور اتوماتیک به سینی پایینی خالی می شود. زمانیکه روغن به سینی پایینی وارد می گردد، تا دمای ۱۰۰ تا ۱۳۰ درجه فارنهایت (۳۸ تا ۵۴ درجه سانتیگراد) خنک شده و به یک تانک دراپ (drop tank) پمپ می شود و از آنجا روغن از یک فیلتر پولیش عبور نموده و به مخزن نگهداری هدایت می شود.
بی بو کننده های نیمه مداوم معمولا اتومات بوده و از یک پنل مرکزی دارای یک کنترلر چرخه زمانی و اینترلاک ها (قفل ها) کنترل می گردد بطوریکه زمانیکه اندازه محموله ناکافی باشد، دریچه تخلیهی (drop-valve) نادرست باز یا بسته باشد، یا روغن به دماهای گرم یا سرد از پیش تنظیم شده در زمان اختصاص داده شده، نرسیده باشد، مراحل متوالی متوقف می گردد.
یکی از مزیت های اصلی سیستم بی بو سازی نیمه مداوم از این امر نشات می گیرد که تمامی سینی ها تحت خلاء بالای نسبتا یکسان قرار دارند.
کل روغن، تیمار یکسانی را دریافت می کند و فضای حلقوی میان سینی ها و پوسته، سیستم را در مقابل اکسیداسیون بواسطه نشت هوا به درون، بیمه می کند.
آرایش بی بوکننده از برگشت جریان مواد نامطلوب یکبار تقطیر شده، به داخل روغن جلوگیری می کند.
این رفلاکس به علاوه هر گونه انتقال مکانیکی، به منظور زهکشی از پایین پوسته بی بوکننده، مجاز می باشد.
توانایی جادادن توده محصول تکرار شونده، با حداقل افت تولید تغییر می کند و عملا عدم وجود اختلاط درونی یک برتری مهم سیستم های نیمه پیوسته نسبت به سیستم های بی بو کننده پیوسته محسوب می شود؛ با این وجود بازیابی حرارت راندمان کمتری نسبت به یک عملیات مداوم داشته و ۱۰ تا ۲۰ درصد بخار بیشتر جهت پاشش مورد نیاز است.
منبع : Fats and Oils: Formulating and Processing for Applications, Third Edition
برای نوشتن دیدگاه باید وارد بشوید.